
Therefore, the 5 Whys analysis aims to inspect a certain problem in depth until it shows you the real cause. This is typical because we often focus on the product part of the problem as we neglect the human factor. You can notice that the root cause of the initial problem turned out to be something completely different from most expectations.įurthermore, it is obvious that it is not a technological but a process problem. Why was he not trained properly? Because CTO believes that new employees don’t need thorough training and they should learn while working.Why was the new developer unfamiliar with all procedures? He was not trained properly.

Why were the developers still working on the new features? One of the new developers didn’t know the procedures.Why were the updates not implemented on time? Because the developers were still working on the new features.Why didn’t we send the newsletter on time? Updates were not implemented until the deadline.
#Fishbone diagram maker software#
Problem: We didn’t send the newsletter about the latest software updates on time. Here is an example of applying the 5 Whys. This is why finding and eliminating the root cause is crucial if you want to avoid iteration of failures. Often, issues that are considered technical problems actually turn out to be human and process problems. Actually, the 5 Whys questions may show you that the source of the problem is quite unexpected.
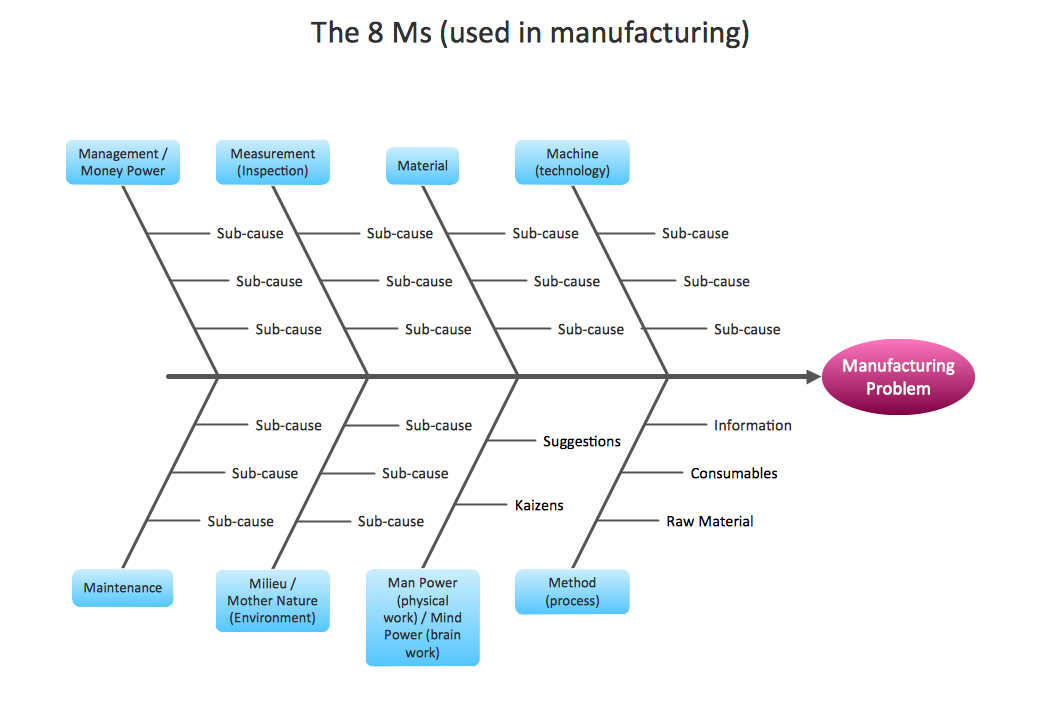
When applying the 5 Whys technique, you want to get to the problem's essence and then fix it. Logically, they can give you the most valuable information regarding any problem that appears in their area of expertise. In other words, the root cause analysis process should include people with practical experience. This means that the decision-making process should be based on an insightful understanding of what is actually happening on the work floor. One of the key factors for the successful implementation of the technique is to make an informed decision. "The basis of Toyota’s scientific approach is to ask why five times whenever we find a problem … By repeating why five times, the nature of the problem as well as its solution becomes clear." Taiichi Ohno Developed by Sakichi Toyoda, a Japanese inventor, and industrialist, the technique became an integral part of the Lean philosophy. The 5 Whys method is part of the Toyota Production System and an essential approach to problem-solving. This interrogative technique is one of the most effective tools for root cause analysis in Lean management. The 5 Whys method allows uncovering the root cause of a problem by simply asking "Why" five times. The good news is that there's a simple yet powerful tool that can help you get to the bottom of any problem: the Five Whys analysis process. This is why your team needs to focus on finding the root cause and tackling it properly. Fixing a problem quickly may be a convenient solution however, it doesn’t protect your work process from recurring mistakes. However, problems are just symptoms of deeper issues. Unpredicted problems occur in any team or process.
#Fishbone diagram maker update#
Integrate with external systems to get the most out of your Kanban softwareĬreate and update cards via email and reply to emails by adding a comment Reduce multitasking, alleviate bottlenecks, and keep a steady flow of work Visualize and track cross-team dependencies via card linksĬustomize your work items as needed and enhance communicationĬreate probabilistic plans for future project deliveryĪutomate your process to trigger actions when certain events occurĪnalyze your workflow’s performance through a variety of Lean/Agile charts
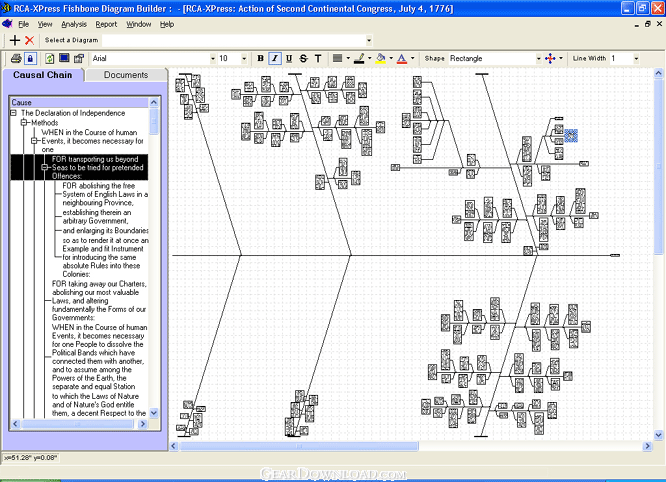
Visualize your past, current, and future initiatives or projectsĭisplay critical business metrics and gather reports in one place Keep track of tasks and get accurate status reports in real-timeĬreate a network of interlinked Kanban boards on a team and management level Keep your teams' work in a single place with multi-layered Kanban boards Monitor business objectives, understand risks, and track the most important performance metrics Implement OKRs and align your strategy with day-to-day executionĭistribute and track work across the entire organization
